Shipping companies will wait less time for their vessels’ propellers with new automated processes established by a German collaboration.
Researchers from the Fraunhofer Institute, along with German moulding specialistsModell- und FormenbauandKUKA Robotics, are developing a robot that can support factory workers when they fabricate large-volume moulds.
Such moulds are used to cast the massive propellers that drive cargo ships across the world’s oceans. These moulds are also used in the renewable energy industry to cast parts for wind turbines.
成型过程历来extremely elaborate and costly because factory workers perform most of the work steps manually.
The use of robots, the Fraunhofer researchers believe, will produce large-volume moulds faster and with less cost. It is claimed an automated process could reduce costs by up to a third.
The Fraunhofer researchers, based at the institute’s factory operation and automation division in Magdeburg, have already developed a KUKA robot that can mill propeller moulds directly out of a compacted sand block. The sand mould is then filled with molten metal to produce the end product.
The research team devised complex software that uses algorithms to calculate and dictate the robot’s optimal milling path and the best-sized diamond cutting tool to carry out the task.
Torsten Felsch, managing researcher at Fraunhofer’s factory operation and automation division, said this robot is already being demonstrated on the factory floor of Modell- und Formenbau.
The Fraunhofer researchers are still working on another KUKA robot that can fabricate models, which serve as a pattern for moulds. The technique would be much more cost effective when multiple identical castings need to be produced because moulds must be destroyed each time a finished casting is extracted.
The robot would replace the manual task of building up models layer by layer. Traditionally, a worker saws out the individual sheets, bonds them atop one another and then machines the shape with a milling machine.
With Fraunhofer’s automated process, a KUKA robot mixes a liquid two-component foam made up of polyurethane and an undisclosed hardening component. It then applies one foam layer after another to the machined surface. Since an average layer is 2cm thick, a rough model of a casting is produced quicker than any manual method.
Felsch compared the process to an additive rapid prototyping technique called fused deposition modelling (FDM). FDM works by melting a plastic filament and extruding it through a heated nozzle. The nozzle moves in horizontal and vertical directions dictated by a numerically controlled mechanism, which is directly controlled by a computer-aided manufacturing (CAM) software package. The next layer is then built on top and the process continues until the entire prototype model is fully built.
Felsch said that unlike regular FDM processes, their rapid layering will not take place in a special workspace with a controlled atmosphere.
‘We want to be able to perform this process in a normal factory environment,’ he added.
The method will also need to be scaled up much more to create the large-scale models needed for ship propeller moulds. Felsch said this will be possible with improved foam-layering techniques and new software to control the process. He said his team should have a factory-floor robot with such capabilities at the end of next year.
German team designs robot for large-volume moulds
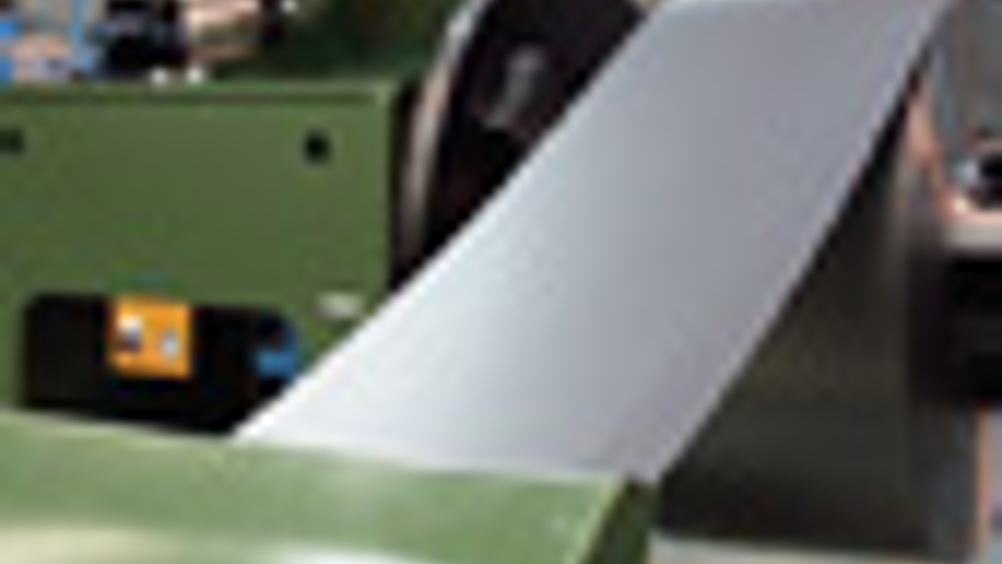
Green transition mineral demands under scrutiny
If this is true then what are the alternatives? How recyclable will these resources be? where is the profit from such invested?