设计高精度零件的最大挑战之一是能够以可重复的方式快速制造它们,以满足非常严格的规格。例如,如果你正在设计飞机发动机燃油喷射器,你需要精确测量的部件,以使飞机机械正常工作,并使乘客将他们的安全托付给航空公司。为了实现这一目标,工程师们不仅要优化特定的部件,还要优化制造过程本身。
增材制造,也被称为3D打印,近年来一直在崛起,作为一种新颖而有前途的方式,可以用更少的材料浪费来制造零件,甚至可以制造以前无法通过传统方法制造的形状。
位于英国考文垂的制造技术中心(MTC)研究增材制造技术,并为航空航天工业的零件生产商提供设计和原型。他们经常使用的一种增材制造方法被称为激光粉末床融合,它使用几十微米厚的粉末层,使用激光一层一层地制造零件。该系统遵循预定义的刀具路径来制造具有非常精细几何细节的零件。
为了验证其增材制造零件的质量和性能,MTC使用COMSOL Multiphysics®软件进行虚拟设计测试、验证和性能预测。在过去的几年里,他们开始从COMSOL模型构建应用程序,使他们能够在不同的团队之间分享他们的分析能力,为他们的客户探索各种项目。
COMSOL在应用程序构建的早期阶段采访了MTC团队(见COMSOL新闻2015).几年后,我们回顾了他们对模拟和计算应用的使用是如何影响他们的设计过程和跨部门工作的。
零件设计的新方法
MTC物理建模团队的负责人Borja Lazaro Toralles告诉COMSOL,激光粉末床融合比其他制造方法具有一定的优势。沉积速率比成形金属沉积工艺慢,但可以获得更高的精度和分辨率。
一个缺点是,当金属冷却时,在建造了几层之后就会发生变形。高温梯度和快速冷却导致的热循环会在沉积过程中产生残余应力。这会慢慢地改变微观结构,从而导致最终零件的扭曲,如图1a所示。
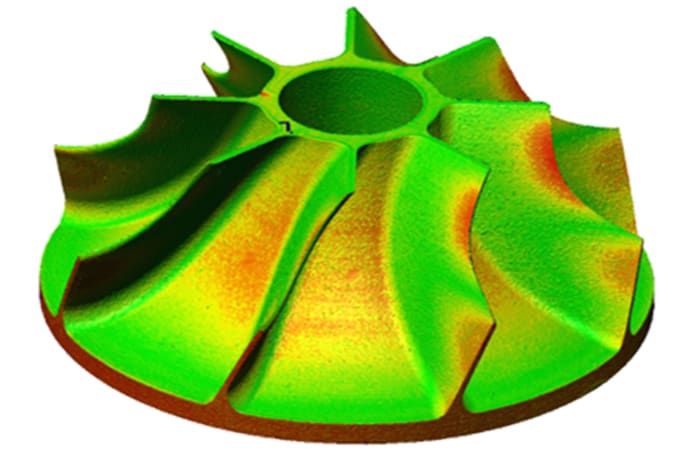
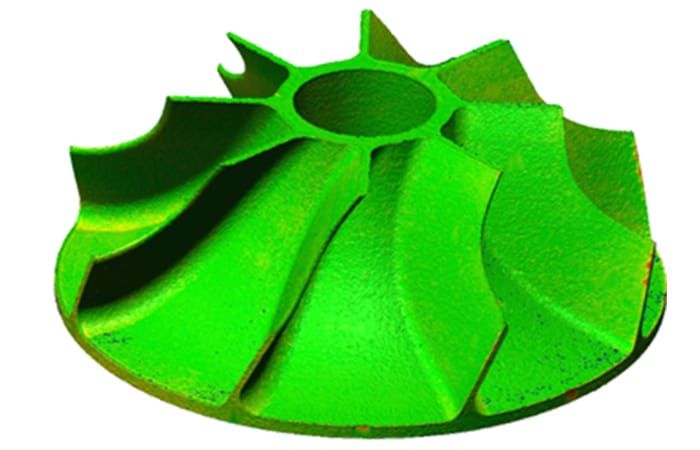
在某些情况下,这些变形可以忽略不计,但在其他情况下,仅仅100微米(0.1毫米)的差异就可能偏离规格太远,使零件无法使用。对于这些情况,MTC团队需要一种方法来绕过热循环的影响。
由于他们无法消除热循环和微观结构的演变,他们采用了另一种方法:“我们创建了一个模拟,预测零件构建过程中的应力和变形,让我们清楚地了解它在打印过程中是如何扭曲的,”Lazaro Toralles开始说。“一旦我们有了这些信息,我们就可以'扭转'零件设计中的扭曲,这使我们能够提前考虑扭曲,从而使最终产品扭曲成我们实际想要的形状。”
这种从错误中逆向工作并将其直接构建到设计中的聪明方法帮助他们更有效地在要求的公差范围内创建零件,因为他们知道预测模型将引导他们产生最小误差的形状(图1b)。
采用多物理场仿真也为增材制造团队与MTC的设计开辟了新的沟通渠道。Lazaro Toralles的团队围绕他们的COMSOL模型构建了一个应用程序,用于预测变形,这使得他们的同事可以运行模拟,并在不完全了解原始模型的情况下查看设计需要更改的地方。
在与部分设计师分享应用之前,团队当然需要构建应用所基于的高保真模型。
复杂多变零件的建模
你如何创建一个能让你测试任何金属形状的模拟?范围是极端的。为了建立一个模型,给设计工程师提供适当的设计调整所需的信息,Lazaro Toralles和他的团队首先定义了一个新的建模过程,可以预测大型部件的最终形状。
“传统的增材制造模型非常详细,直到微观结构。但由于计算成本的原因,这些不适合模拟大型部件的构建,”他告诉我。“他们花了很长时间。但我们仍然需要了解整个部件在打印过程中的表现。为了避免这种情况,我们将打印构建的层“合并”,并根据实验数据施加分析温度场。这减少了求解时间,但仍能给出准确的解。”
由于MTC使用各种金属,从航空级钛到不锈钢,因此他们在COMSOL模型中参数化输入,例如材料特性,集总层厚度,零件上的构建板固定装置和网格单元尺寸,以便他们可以使用该模型测试许多形状,尺寸和材料的零件。
在COMSOL®软件环境中,他们使用结构力学功能来定义具有温度依赖性塑性和热膨胀的线弹性材料,使用分析温度场。该应用程序还执行几个自动化CAD操作,为合适的“集总”分层准备几何形状。
然后,模拟生成一个网格来表示一个近似的工具路径,因为层的集总使得使用真实的网格变得不切实际。温度场被施加到网格点上。然后,软件计算沉积过程中产生的应力,并预测零件的最终形状(图2)。
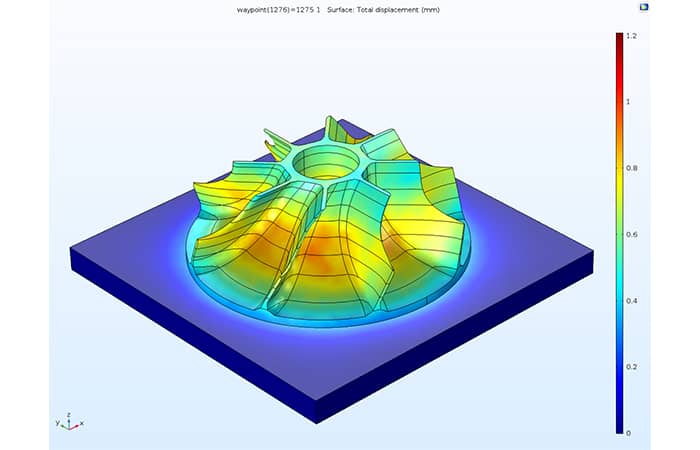
传播预测能力
一旦模拟预测了特定部件的错误,那么以一种清晰而简洁的方式将信息传递给设计团队就是另一回事了。许多公司已将其建模团队分为设计和模拟两部分,这得益于专门从事其中一项工作的员工。但这在零件设计和零件分析之间留下了一个空白。
应用程序通过允许模拟专家将他们的模型打包到用户友好的界面中来弥补这一差距,设计人员可以使用这些界面来运行他们自己的测试,而无需了解下面模拟的所有复杂性。这使得设计工程师可以更轻松地进行调整,并节省了仿真专家在每次需要评估新零件性能时运行分析的时间。
设计团队使用各种CAD平台创建了许多复杂的部件,因此COMSOL模型和相应的应用程序需要非常强大。它包括CAD导入功能,因此可以测试任何形状。这对于有机形状尤其重要——那些基于植物、动物和地形等自然特征的形状——比如在Rhino等程序中绘制的形状。
该应用程序是用COMSOL Multiphysics中提供的Application Builder创建的,可以显示模拟结果-给定部件的最终形状,变形和应力水平,在本例中是飞机叶轮(图3)。
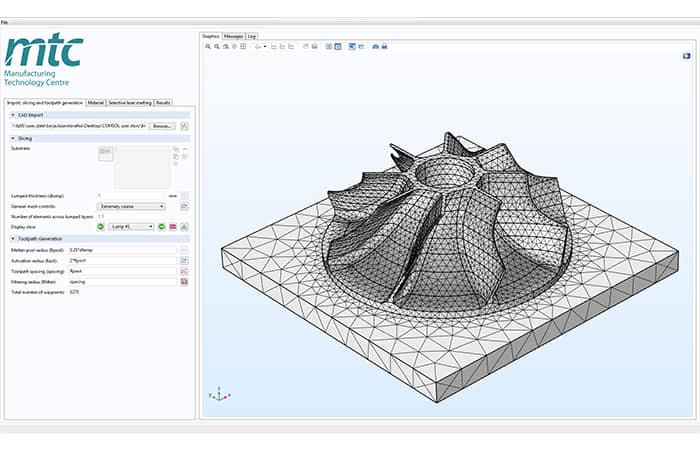
Lazaro Toralles补充道:“我们(模拟团队)经常自己使用这款应用。“一旦我们建立了它,在应用程序中做一些输入改变就容易多了,而不是回到原来的模型。但设计团队并不从事模拟工作。这个应用程序是为他们设计的,因为它允许他们导入零件模型,并检查在打印过程中如何弯曲的预测。”
COMSOL Multiphysics中包含的Application Builder允许Lazaro Toralles完全控制应用程序用户可用的内容。随着应用程序根据公司的新需求不断发展,他一直小心翼翼地构建必要的输出和显示,并锁定某些输入和条件,以便应用程序用户不会无意中产生错误。底层的模型设置对用户来说仍然是隐藏的,但是模拟功能已经扩展了。
巩固新的合作
Lazaro Toralles通过COMSOL Server™产品部署应用程序,用于分发、管理和运行模拟应用程序。在网上托管这款应用程序,可以让公司任何地方的同事都可以访问它。
模拟改变了MTC团队合作的方式。现在,他们有了一个既定的程序,设计师和仿真工程师能够快速沟通,轻松测试设计,并进行更改,从而为客户提供所需的原型,以便大规模生产。
Lazaro Toralles承认,当他们最初开始向其他部门提供模拟应用程序时,有人持怀疑态度。“我们必须赢得他们的信任。但由于该模型一直提供良好的结果,每个人都发现它很有帮助。这款应用程序包含了一切:它可以切割打印几何形状,显示网格,指导工程师进行失真分析,并提供反馈。”他们的模拟工作是帮助MTC建立工作流的重要组成部分,该工作流可以改善物理建模团队和设计团队之间的沟通。这最终改变了他们处理零件设计的方式。
Borja Lazaro Toralles, MTC物理建模部候任技术经理
美国公司声称“超低碳”蓝色氢工艺
这与蒸汽甲烷重整完全相反。在中间的某个地方,亚化学计量技术,如部分氧化或自动热重整可能更有效……