电机是迷人的,因为它们能够把电能转换成机械能,然后再转换回来。例如,在电动汽车中,这种双向转换被用来在行驶时提供牵引力,在制动时提供再生。
这种再生技术可以将行驶车辆的动能转化为可用的电能并储存在电池中,而不是像传统的机械摩擦刹车那样作为热量浪费掉。
在电气和机械领域之间高效转换能源的能力使电机成为汽车、航空航天、工业和能源部门正在进行的电气化努力的核心,以追求我们2050年的碳净零目标。
的英国航空航天技术研究所而且先进推进中心(APC)它们分别代表了航空航天和汽车行业的未来技术需求,要求到2035年电机功率密度在9至25千瓦/公斤之间,与目前的2至5千瓦/公斤形成鲜明对比,即使使用最先进的永磁材料(如钕铁硼)、电工钢(如CoFe)和高性能电绝缘铜绕组。
不幸的是,电学和机械领域之间的能量转换过程并不是100%有效的。一些能量被“损失”了,因为它被转化成不受欢迎的形式,如噪音、振动,主要是热。
热是由轴承中的机械摩擦、电钢和磁体中的滞后和涡流效应以及绕组导体中的焦耳效应和涡流效应产生的。其中,线圈往往是主要的热源。这增加了元件的温度,通常由导体的电绝缘材料施加的温度限制。
当设计高功率密度的电机时,我们必须平衡额定功率、质量和体积与产生的热量和由此产生的温升-小心不要超过设计限制。通过减少绕组产生的热量,加强热管理,有效地冷却绕组,提高导体电绝缘额定温度,可以提高功率密度。
传统的绕组是由圆柱形或矩形截面的导体通过拉丝工艺制成的,最早记录在12世纪th世纪西奥菲勒斯。导体束可以用来减轻蒙皮效应,或仔细调换形成利茨型绕组,以平衡链电流和减少总损耗。可获得的截面形状的有限范围和在整个绕组中使用单一导体类型的必要性是提高性能的障碍。
绕组通常通过安装在定子上的收缩式液体冷却装置进行冷却,在那里,导体中产生的热量必须穿过电气绝缘系统、电气钢和几个热差材料界面,才能到达流体。为了改善这一点,可以在绕组上直接训练喷雾冷却射流来增强传热,但代价是复杂性。
导体电绝缘涂料是典型的有机聚合物,由于其高介电强度,机械柔韧性和韧性,非常适合制造中经常使用的艰巨的机械缠绕过程。然而,高温额定值为180 - 240o对热点温度有明确的限制,并禁止在极端温度环境中使用。
采用金属AM工艺可以同时满足减少产生热量、改善热管理和提高电气绝缘极限温度这三个设计目标。
替代传统制造工艺的一种方法是采用金属增材制造(AM),在这种方法中,粉末材料或原料在连续的二维层中有选择地粘合,以逐步形成3D零件。
迄今为止,铜、铜合金和铝合金绕组已经利用了AM -或更具体地说LBPF工艺-展示了几个优点。一个关键的优点是AM过程的几何自由度。这不仅可以使每个导体的形状最佳,而且可以使用目标减损技术。例如,在绕组开始时的导体可以是实心的,然后过渡到绞线,转置束。因此,最有益的导体类型和拓扑结构可用于绕组的每个部分。
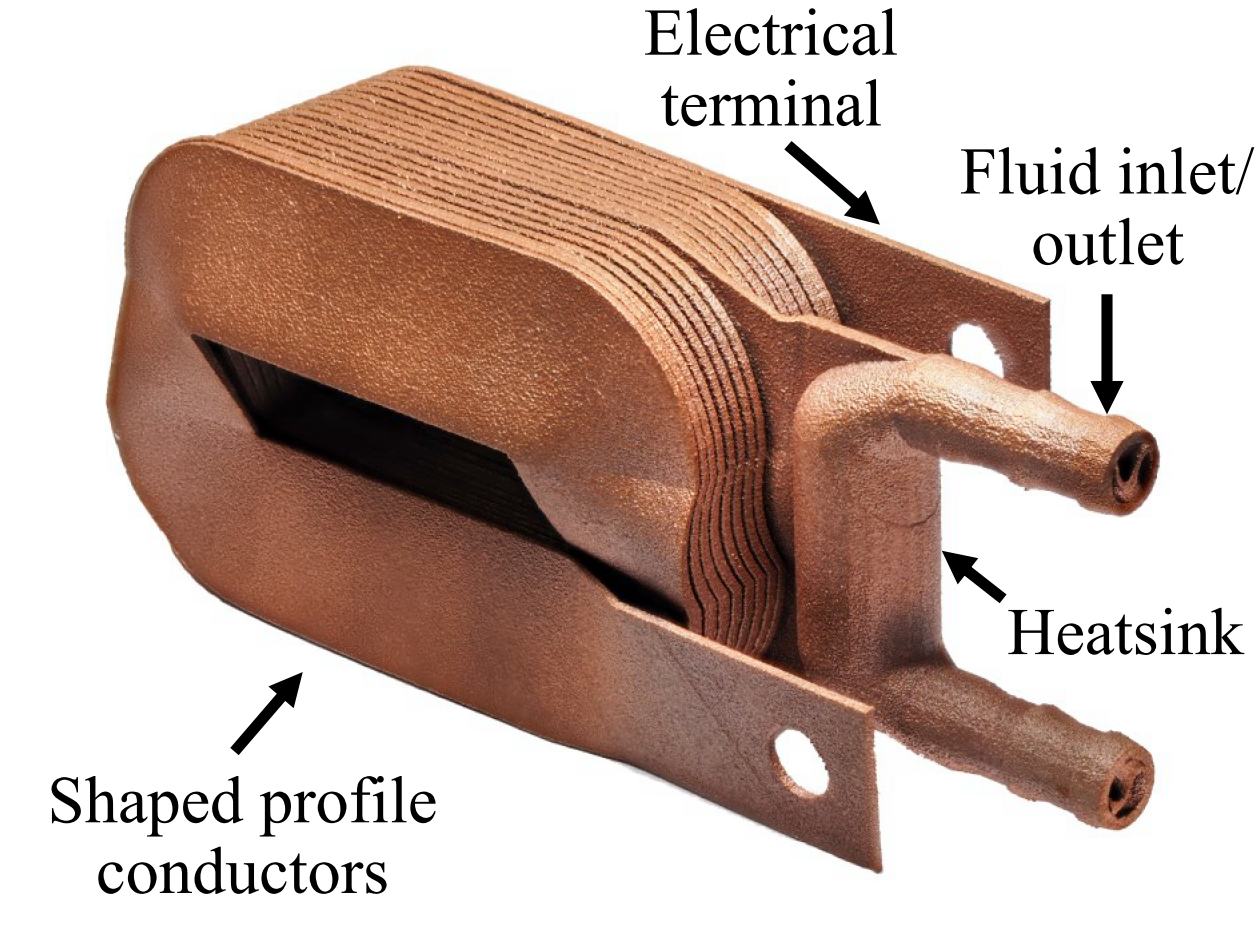
另一个重要的优势是新的冷却方案的可能性。例如,可以将液冷通道战略性地嵌入到导体中,或将末端绕组进行雕刻,以最小化体积和最大化热传递。复杂晶格和周期性填充结构可以用来形成有效的热交换器,在不侵占导电截面的情况下冷却导体。
使用AM工艺,绕组在其缠绕状态下有效地制造,消除了绝缘涂层承受大量机械负载的需要。因此,可以采用陶瓷等替代高温材料来解决热极限问题。
从本质上说,采用金属AM工艺可以同时满足减少产生热量、改善热管理和提高电气绝缘温度限制这三个设计目标。因此,可实现的功率密度的逐步变化可以实现,使我们更接近9 - 25千瓦/公斤的目标,以追求2050年的碳净零。
尼克·辛普森博士是高级讲师和UKRI未来领袖研究员布里斯托大学在那里,他创立了电机工厂,专注于将增材制造引入高性能电机的设计。
如果你想听到更多来自AM领袖、远见者和创新者的信息,请参加我们在诺丁汉举办的今年的添加剂国际峰会,13-14日th7月。访问https://www.additiveinternational.com/为更多的细节。
Kwarteng公布刺激措施以促进经济增长
如果他想帮助 的小型企业,他应该重新考虑适用于非相邻继承的商业费率的神秘规则